Nel corso di un’attività pluridecennale TCM Plast ha accumulato un patrimonio di conoscenze sullo stampaggio ad iniezione e può condividere la propria esperienza sia nella fase di progettazione dello stampo che nella definizione delle specifiche tecniche del processo di stampaggio.
La progettazione del pezzo, la scelta del polimero e la realizzazione dello stampo sono normalmente a carico del committente.
TCM Plast in questa fase può assistere il committente nella realizzazione dello stampo per la scelta dei punti di iniezione, lo sformo ottimale del pezzo, la determinazione dello spessore, il mascheramento delle linee di divisione.
Inoltre TCM Plast può assistere il committente per definire le specifiche di stampaggio del pezzo e risolvere eventuali problematiche del processo di stampaggio ad iniezione: il modo in cui la plastica fusa entra nella cavità dello stampo, la riempie e si raffredda al suo interno per formare la parte può causare problemi di sollecitazione, segni di avallamento ed altri difetti comuni dello stampaggio come bolle, bruciatura, bave, ecc.
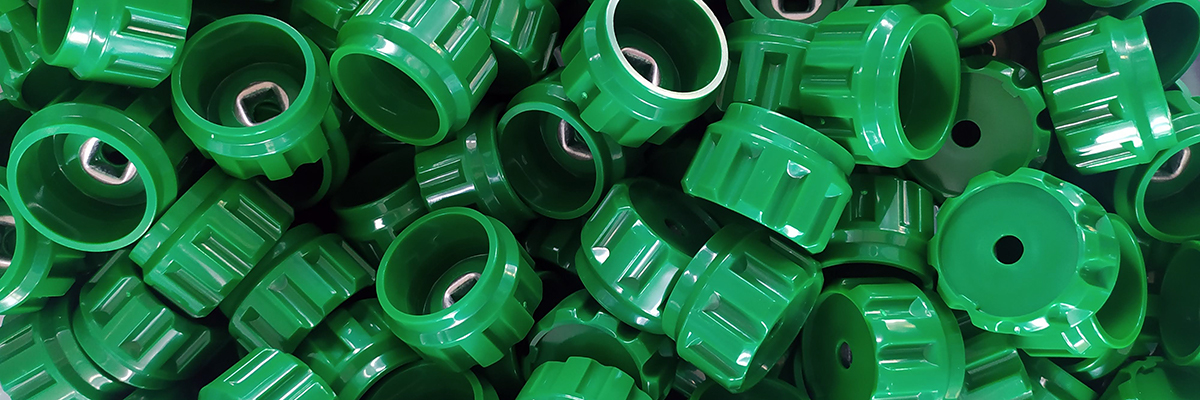
APPROFONDIMENTO
Pregettazione stampo
1) Punti di iniezione
Il tipo di punto di iniezione, il design e la posizione possono avere effetti sul riempimento dello stampo e la determinazione di difetti come avallamenti, sulla rimozione del punto di iniezione o sull’aspetto della parte stessa, sulle dimensioni della parte e la sua distorsione.
Esistono diversi modi di posizionamento dei punti di iniezione, a seconda della dimensione e della forma della parte.
Il punto di iniezione laterale rappresenta il design più comune ed è ideale per parti piatte.
Il punto di iniezione inferiore (Sub Gate) offre maggiore flessibilità di posizionamento del punto stesso in una posizione ottimale sulla parte.
Il punto di iniezione caldo è ideale per forme arrotondate e coniche in cui è necessario un flusso uniforme.
Il punto di iniezione diretto o mediante materozza. I punti di iniezione diretti sono i più facili da progettare. Le parti con punti di iniezione diretti sono soggette a minori sollecitazioni e sono caratterizzate da un’elevata resistenza.
La posizione dei punti di iniezione deve ridurre al minimo le ostruzioni nel percorso del fluido allo scopo di ridurre il tempo di riempimento.
2) Sformo
Per il rilascio corretto della parte quando lo stampo viene aperto, le pareti laterali dello stampo vengono rastremate nella direzione di apertura. Tale rastremazione viene anche chiamata “sformo”. Tale sformo consente alla parte di liberarsi dallo stampo non appena lo stampo viene aperto. La quantità di sformo necessaria può dipendere dalla finitura superficiale dello stampo. Una superficie dello stampo liscia e lucidata consentirà un’espulsione della parte con minore sformo.
3) Spessore della parete
Prima dell’espulsione, le parti stampate per iniezione vengono adeguatamente raffreddate in modo che mantengano la forma una volta scaricate. Durante la fase di raffreddamento nel processo di stampaggio, le variazioni di pressione, velocità e viscosità plastica devono essere ridotte al minimo per evitare difetti. Vi sono alcuni aspetti maggiormente importanti in questa fase rispetto allo spessore delle pareti. Questa funzionalità può influire pesantemente sui costi, sulla velocità di produzione e sulla qualità delle parti finali.
Scegliere lo spessore della parete adeguato per la parte può avere effetti molto importanti sul costo e sulla velocità di produzione. Sebbene non vi sia alcun tipo di limitazione sullo spessore delle pareti, lo scopo di solito è di scegliere lo spessore minimo possibile. Una parete più sottile utilizza meno materiale, il che riduce i costi e richiede un tempo minore per il raffreddamento, riducendo così il tempo di ciclo.
Le sezioni spesse richiedono un tempo di raffreddamento maggiore rispetto a quelle sottili. Durante il processo di raffreddamento, se le pareti presentano spessore non costante, le pareti più sottili si raffreddano prima mentre le pareti spesse sono ancora in fase di solidificazione. A mano a mano che la sezione spessa si raffredda, questa si ritira intorno alla sezione più sottile già solida. Ciò causa la deformazione, la distorsione o la fessurazione in corrispondenza dei punti di incontro delle due sezioni. Per evitare questo problema, è necessario provare a progettare parti con pareti completamente uniformi. Quando non sono possibili pareti uniformi, la modifica dello spessore deve essere quanto più graduale possibile.
4) Linee di divisione
Una “linea di divisione” è una linea di separazione sulla parte in corrispondenza del punto di incontro delle due metà dello stampo. Tale linea indica in realtà il “piano” di separazione che attraversa la parte. Sebbene nelle parti semplici questo piano può essere una superficie semplice e piatta, si tratta spesso di una forma complessa che traccia il perimetro della parte attorno alle diverse caratteristiche che formano la “silhouette” esterna della parte stessa. Le linee di separazione si possono riscontrare anche nel punto di incontro di due pezzi qualsiasi di uno stampo. Le linee di separazione non si possono evitare: sono presenti in ogni parte. Durante la progettazione di una parte, è necessario tenere presente che il materiale fuso fluirà sempre in direzione della linea di separazione perché è il punto in cui è più facile che avvenga la fuoriuscita o lo “sfiato” dell’aria spostata dal riempimento.
Specifiche di stampaggio
1) Sollecitazione
Il principale nemico di qualunque parte in plastica stampata per iniezione è costituito dalle sollecitazioni. Quando una resina plastica (che contiene lunghe catene di molecole) viene fusa nella fase di preparazione per lo stampaggio, il calore e la forza di taglio dell’estrusore spezzano temporaneamente i legami molecolari, consentendo così alle molecole di passare nello stampo. Utilizzando la pressione, la resina viene spinta nello stampo, andando a riempire ogni singola parte di esso. Man mano che le molecole vengono spinte a riempire ogni particolare dello stampo, vengono costrette a piegarsi e distorcersi per andare a formare la parte da realizzare. Percorrere angoli molto acuti comporta maggiori sollecitazioni sulle molecole, rispetto ai percorsi lineari o con angoli ampi. Inoltre, anche il passaggio brusco da una caratteristica all’altra comporta sollecitazioni elevate per le molecole.
Mentre il materiale si raffredda e i legami molecolari riportano la resina allo stato solido, le sollecitazioni vengono “bloccate” nella parte. Le sollecitazioni/stress relative alla parte possono causare deformazioni, segni di affossamento, fessurazioni, rotture premature o altri problemi.
Sebbene alcune sollecitazioni in una parte stampata a iniezione siano prevedibili, è necessario progettare le parti in modo da ridurre le sollecitazioni il più possibile. Alcuni modi di farlo prevedono l’aggiunta di transizioni dolci e regolari tra le varie caratteristiche nonché l’utilizzo di parti arrotondate e raccordi nelle aree potenzialmente soggette a sollecitazioni elevate.
2) Segni di avvallamento o risucchio
Quando la sostanza fusa fluisce nello stampo di iniezione, le sezioni spesse non si raffreddano con la stessa velocità del resto della parte poiché il materiale più spesso viene isolato dalla superficie esterna della plastica a raffreddamento più veloce. Quando si raffredda la parte interna, si restringe con una velocità diversa rispetto al rivestimento esterno già raffreddato. Questa differenza della velocità di raffreddamento causa una ritrazione verso l’interno che determina un segno di risucchio sulla superficie esterna della parte, o peggio, la deforma completamente. Oltre ad essere poco accattivante, il segno di risucchio rappresenta inoltre una sollecitazione aggiuntiva presente nella parte. Altre aree meno visibili dove possono verificarsi questi problemi sono gli angoli, nervature, parti rialzate.
Un modo di evitare segni consiste nella eliminazione del materiale interno nelle sezioni solide della parte per ridurre lo spessore delle pareti. Se la resistenza di una parte solida è una condizione indispensabile, è possibile utilizzare una trama di nervature all’interno dell’area cava per aumentare la resistenza ed evitare segni di affossamento sul pezzo.
3) Altri difetti comuni dello stampaggio
Lo stampaggio a iniezione è una tecnologia complessa con potenziali problemi di produzione. Tali problemi possono essere causati da difetti dello stampo o più spesso dalla procedura di stampaggio.
Bolla Formazione di bolle o zone elevate o a strati sulla superficie della parte in plastica.
Causa: stampo o materiali troppo caldi, spesso causati da un raffreddamento insufficiente intorno allo stampo o da un riscaldatore difettoso
Segni di bruciatura Bruciatura da aria/gas Aree bruciate nere o marroni sulla parte in plastica situata nei punti più lontani dal punto di iniezione.
Causa: mancata ventilazione dello stampo, velocità di iniezione troppo alta
Delaminazione Sottili strati simili alla mica che si formano sulla parete della parte.
Causa: contaminazione del materiale ad es. PP mescolato con ABS, cosa molto pericolosa se la parte viene utilizzata per una applicazione in cui la sicurezza è fondamentale, poiché il materiale che si delamina presenta una resistenza molto bassa per l’impossibilità di legare i materiali
Bave Materiale in eccesso in uno strato sottile che supera la geometria della parte.
Causa: Stampo danneggiato, velocità di iniezione eccessiva o troppo materiale iniettato, forza di serraggio troppo bassa. Il problema può essere inoltre causato da sporco o contaminanti sulle superfici di chiusura dello stampo.
Linee di flusso. Linee o motivi ondulati “off tone”.
Causa: velocità di iniezione troppo bassa (il materiale plastico si è raffreddato troppo durante l’iniezione, le velocità di iniezione devono essere impostate in tutti i casi sui valori massimi possibili)
Segni di risucchio Depressione localizzata
Causa: tempo di mantenimento/pressione troppo basso/a, tempo di raffreddamento troppo breve, con rami di colata caldi senza materozza. Ciò può essere causato dalla temperatura del punto di iniezione troppo alta
Stampata incompleta. Mancato riempimento. Parte parziale.
Causa: Mancanza di materiale, velocità di iniezione o pressione troppo basse
Segni di striature. Segni di schizzi e/o striature.
Causa: motivo circolare intorno al punto di iniezione causato da gas caldo o umidità presente all’interno del materiale, di solito dove le resine si sono asciugate in modo non corretto
Segni di filamenti. Raccordature.
Causa: Presenza in una nuova operazione di iniezione di segni relativi a operazione precedente. Temperatura ugello troppo alta. Il punto di iniezione non si è raffreddato
Sfiati Spazio vuoto all’interno di una parte (sacca d’aria)
Causa: Mancanza di pressione di mantenimento (la pressione di mantenimento viene applicata durante il tempo di attesa). Inoltre lo stampo potrebbe essere non ben registrato ovvero le due metà non sono ben centrate e le pareti della parte non presentano lo stesso spessore.
Linea di unione/fusione Linea scolorita in corrispondenza del punto di incontro di due parti frontali
Causa: le temperature del materiale/dello stampo sono troppo basse (il materiale è freddo al momento dell’unione, con la conseguente mancata unione)
Deformazione Parte distorta
Causa: Raffreddamento troppo breve, il materiale è troppo caldo, mancanza di raffreddamento dello stampo, temperatura acqua non corrette (la parte si piega all’indentro verso il lato caldo dello stampo)