We are specialised in injection moulding.
The tonnage of our machine presses goes from 10 to 200 tons.
The weight of the final components goes from less than 1 gram to 400 grams.
All the presses are managed by robotic arms.
Technical details
Below are the details of our production processes
Injection moulding machine
Injection moulding machines, also known as injection presses, consist of a hopper, an injection piston or screw plunger, and a heating unit. The mould is fixed on the work surface of the moulding machine, and the molten plastic is injected into it through a casting hole.
The presses are sorted according to the clamping force they can exert. The clamping force makes sure the mould remains closed during the injection process. The required amount is determined by the projected area of the piece to print. Or based on the material and the size of the part: for example, larger plastic pieces require a higher clamping force.
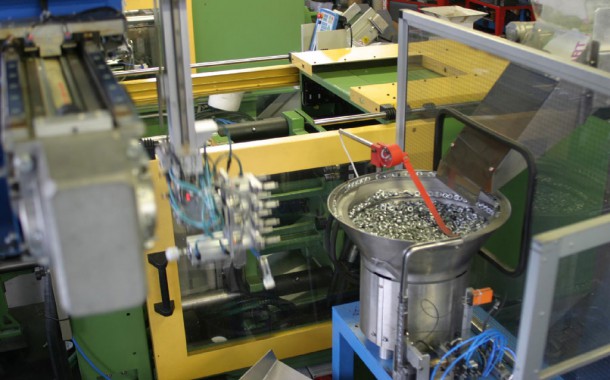
Mould:
A mould is a tool used to produce plastic parts. These components are a mechanical wonder, made of hardened steel, pre-hardened steel, aluminium and/or a beryllium-copper alloy. The material choice is purely of an economic nature. Steel moulds are generally more expensive but also more durable. They amortize the higher initial cost on a higher number of produced parts Aluminium moulds are less resistant and mainly used for low production volume. They usually cost less than their steel counterparts, but it depends on the type of geometric shape.
Injection moulding
During the injection moulding process, plastic granules are conveyed from a hopper into a heated cylinder. As the granules slowly flow inside the hot plasticizing cylinder – driven by a rotating helical screw called auger conveyor – they melt. The molten plastic enters the mould cavity through a casting hole. The mould maintains a pre-set temperature so the plastic can solidify as soon as the mould fills.
The cycle of injection moulding
The sequence of events during the injection mould of plastic part is known as the injection moulding cycle. The cycle begins when the mould closes, followed by the polymer injection into the mould. Once the cavity is filled, a holding pressure is exerted to compensate for volumetric variations in the material. In the following step, the screw retracts to let the plastic granule inside the cylinder and prepare for the next production After the cooling time, the press opens the mould, and the plastic piece is ejected.
Mould finishing
The mould surface can have a glossy or opaque finish. Special finishes are developed during the design phase.